FRAC SAND PROCESSING & RAIL LOADOUT - CHIPPEWA FALLS, WISCONSIN
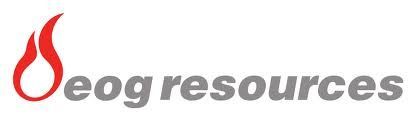
Matrix Engineering provided PLC programming and network communications for a Frac Sand Processing and Distribution Facility in Wisconsin. In particular Matrix worked with Pebco who provided the required gates and loading spouts to transfer 3 different grades of dried frac sand from the process to a high speed railcar loadout facility.
The storage facility consists of (12) 5700 ton silos each having 6 discharge gates and a series of belt conveyors for transferring stored material for distribution via 100T railcars. Above the rail loadout are (4) separate bins each having (2) rolling variable gates and dustless loading spouts serving (2) individual rail lines. Each car is filled from both discharge variable rolling blade gates simultaneously onto rail scale maintaining high accuracy and less than a 1% differential between car axles. Filling rates are in the range of 30 – 40 tons per minute.
Matrix worked with an AB ControLogix platform with (15) PLC racks and (4) DeviceNet Motor Control Centers to control the conveyor motors, gates and all associated equipment. Communication networks for this system are ControlNet, DeviceNet, and Ethernet. Part of our scope within the load-out controls is collecting data on the specific car and batch cycle and pass this information on to the DCS Wonderware HMI and Historian.