Projects
Pulverized Fuel Systems
Matrix has developed and patented a unique method for precisely and predictably delivering a powdered fuel for optimal combustion. We have deployed this system with ground petroleum coke for burning in lime recovery kilns commonly found in pulp and paper mills.
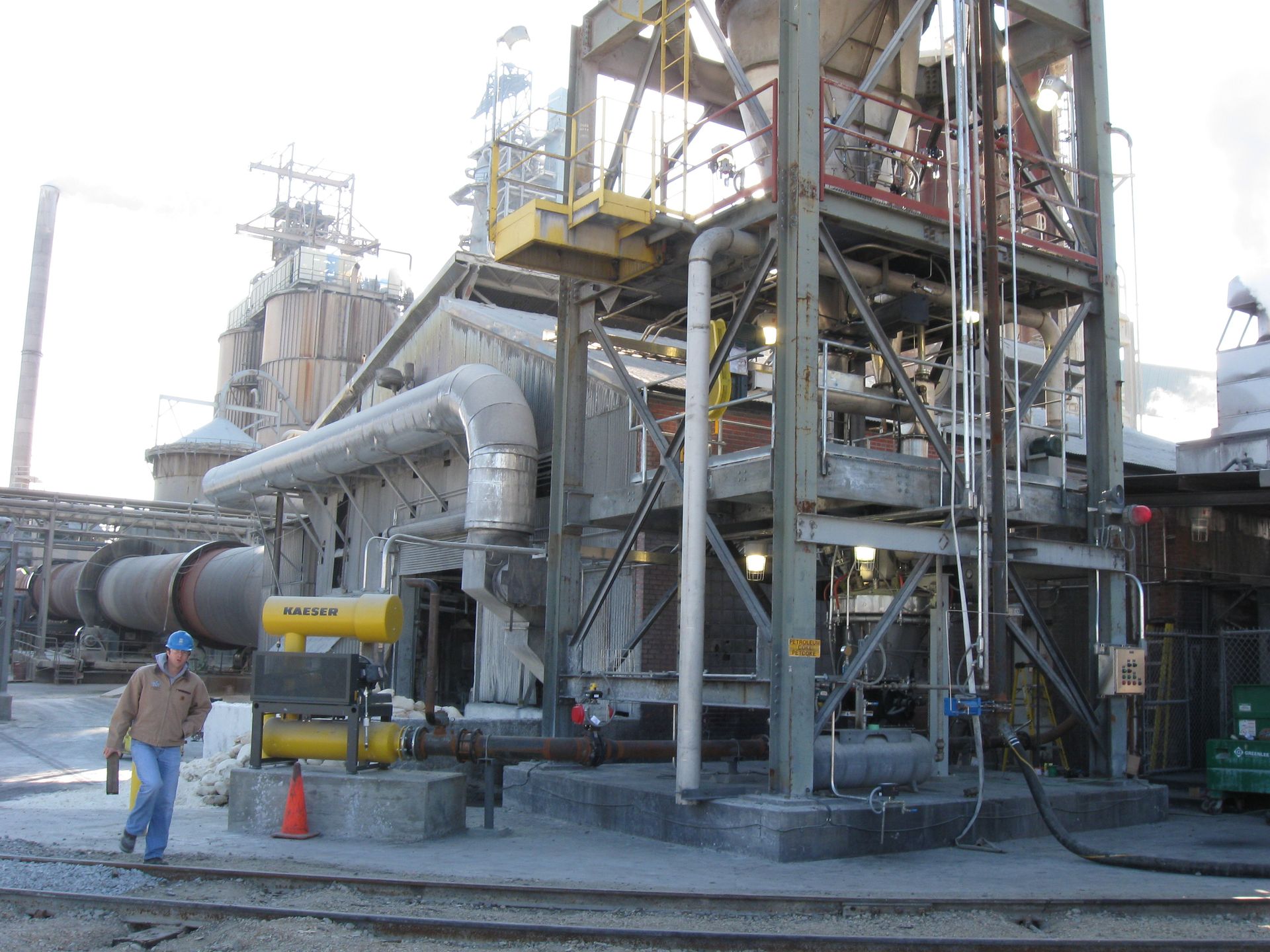
Matrix received a contract for the engineering and equipment necessary to upgrade an existing petcoke feed and convey system. The Matrix System will more than triple the petcoke feed rate and provide instantaneous feedback on system performance. The existing silo was re-used and retrofitted with the Matrix DENSI-FEED system. We also replaced the existing convey system and instrumentation for delivering the petcoke to the Andritz burner nozzle.
Matrix provided the complete system engineering and equipment supply package for IP in Prattville, AL. This mill actually pioneered coke burning in lime kilns back in the 1980's. However, this first petcoke system was a direct-fire unit which received raw coke into a pulverizer and blew it directly to the kiln burner. As it turned out, this method was very difficult to control since nearly all of their combustion/primary air into the kiln was required to convey the coke out of the pulverizer. As a result, they could not burn as much as they wanted and their kiln lacked turn down and the ability to optimize or flame shape and good CaO production. At the time our our project, we also engineered a full pulverizer replacement using a Williams Crusher. However, we instead directed the outflow of the pulverizer to our 180T Storage Silo with DENSI-FEED System below. Currently they are able to fire petcoke and natural gas and are feeding at rates as high as 200 tons per hour (60 MMBtu/hour).
Matrix provided the complete system engineering and equipment package for J K Paper Limited, Unit: JKPM. This was the first installation in India for petcoke fuel burning in a Lime Recovery Kiln and it was a tremendous success. Our DENSI-FEED pulverized fuel system is performing flawlessly alongside fuel oil at 65-70% substitution levels in a kiln capable of 300 mtons CaO per day. This system was designed to accept petcoke from a bulk bag delivery into a 240 mton silo. Also, of significant importance, Matrix delivers the fuel through our delivery convey system burner over 650 ft (200m) away. In addition to our patented system, Matrix provided construction management, commissioning and on-site training services for the mill. Matrix also provided the burner for this non-domestic system, taking full responsibility for the complete reliability and success of the system including process fuel substitution performance guarantees. The Mill has been extremely pleased with our petcoke fuel system performance as well as their lime kiln production and the fuel conversion.
Matrix was awarded a contract to provide a pulverized petcoke fuel delivery system for one kiln utilizing a truck/railcar unloading system, storage silo, feed system, pneumatic conveying system, and all the necessary instrumentation. We successfully commissioned this project in October 2008. The system utilizes natural gas and petcoke. The petcoke system provides 90 MMBtu/hour (3.0 tons per hour) to the kiln using a Coen burner. Although the mill itself is located in Luke, Maryland, the Lime Kiln is located next to it in West Virginia on the banks of the beautiful Potomac river. The 90ft long silo was actually delivered in one piece along mountain roads to be placed near the firing end of the kiln.
Matrix provided the system engineering and critical equipment package for Smurfit-Stone in Panama City, Florida. This system was designed to accept petcoke from trucks and feed a lime kiln burners from a 180 ton silo. A pneumatic conveying system with a variable rate blower delivers petcoke to the burner in accordance with their specific air flow requirements. Control of the Matrix system was integrated into their existing DCS. Using the Matrix DENSI-FEED System they were able to co-fire petcoke with fuel oil or natural gas and are feeding at rates as high as 3.80 tons per hour (115 MMBtu/hour).
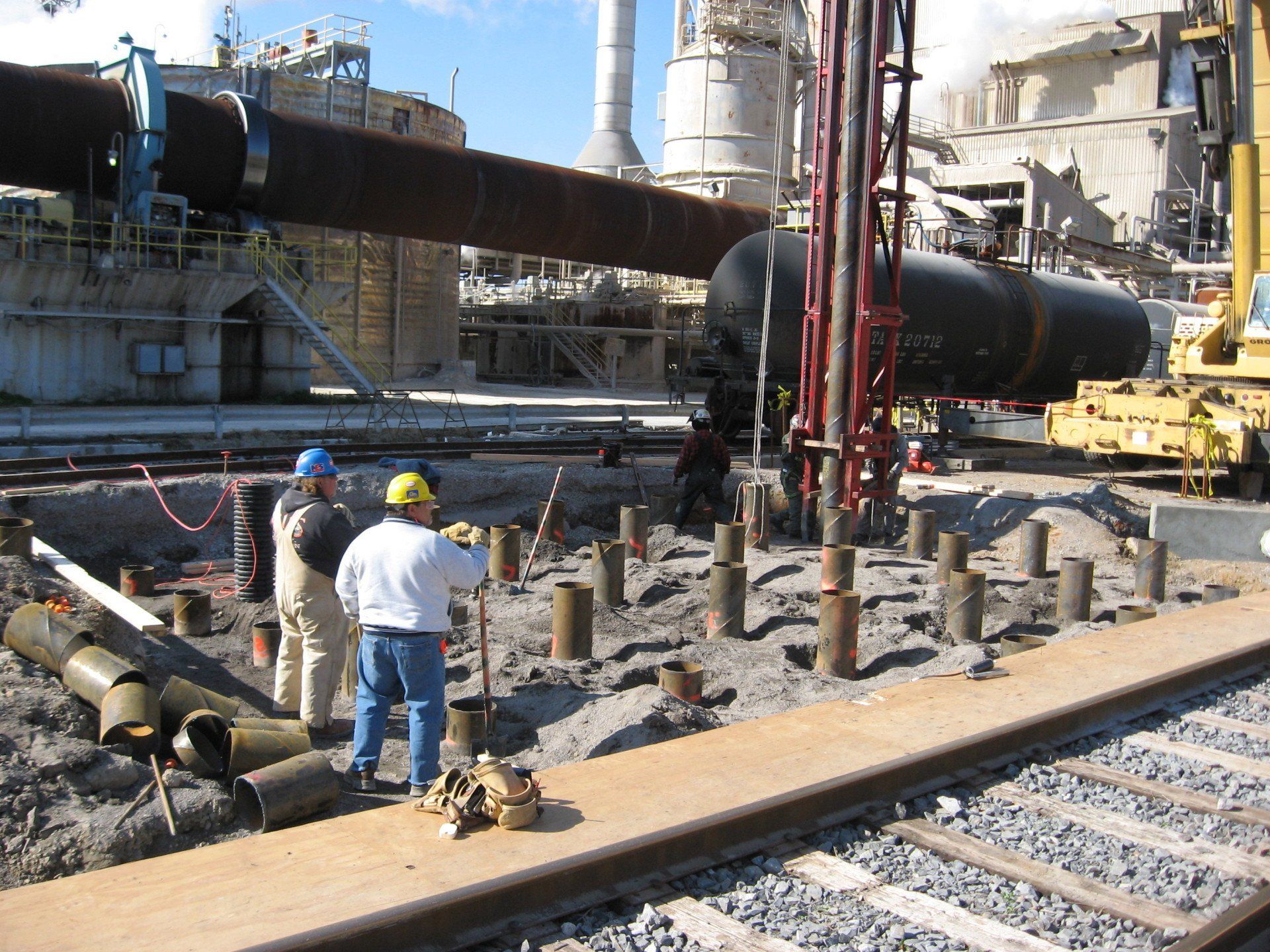
Matrix was awarded a complete turnkey contract for engineering, equipment supply, and installation of a single discharge storage silo and petcoke feed system for NewPage Corp. in Wickliffe, Kentucky. The system is capable of unloading both truck and rail to fill the silo and co-fired petcoke with natural gas on a KFS burner. Matrix provided the turnkey installation packages and on-site construction management for civil/foundation, structural, mechanical and electrical contracts. As a result, s tartup for this project was completed 2 months ahead of schedule in May 2007. Completing this in record time saved the mill over $200K during a time of high natural gas prices.
Matrix provided the system engineering and critical equipment packages with silo for a dual discharge petcoke delivery system at GP Cellulose in Perdue Hill, Alabama. This system was designed to accept petcoke from pneumatic railcars or trucks and feed two lime kiln burners from a common 180 ton silo. A dual discharge hopper bottom was specifically designed for two petcoke DENSI-FEEDERS, though initially, GP chose to implement the project in two phases and only installed one of the two feed systems. Matrix commissioned the second kiln feed line 2 years later. A stepped convey line and 100hp blower was used on the rail unloading system for a record unloading time of 2 hours for 100tons at a distance of 200ft away. A pneumatic conveying system with a variable rate blower delivers petcoke to the burner in accordance with the specific air flow requirements for flame shaping. Control of the Matrix system was integrated into the mill's existing DCS. The system is able to co-fire fire petcoke, fuel oil, natural gas or tall oil. The first kiln’s system at was proven and tested to 3.0 tph with natural gas and successfully burned in excess of 2.4 tph of petcoke in combination with fuel oil. Below is a picture of the flame at 2.5 tph with fuel oil.
Matrix implemented an engineering and equipment supply contract for a storage silo and petcoke feed system for Weyerhaeuser in Springfield, Oregon. The system consisted of a 180 ton storage silo and a variable feed system specifically designed for the discharge of ground petcoke. A variable rate blower was used to transfer the petcoke approximately 350 feet to the existing “coke-ready” burner. All controls and display panels were integrated into the mill’s existing DCS system. Matrix provided the civil/structural, mechanical, and electrical engineering for the project. System startup was conducted in December 2006.